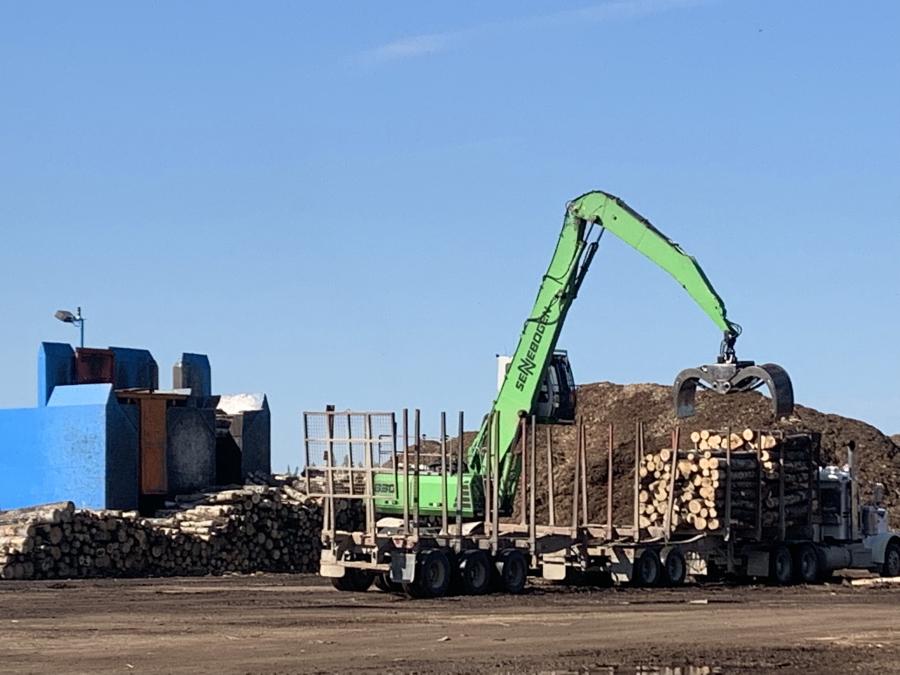
Tue September 20, 2022
Sennebogen
They just keep going. And going. And going.
When Larry McKay took over Mountainside Unloading in 2006, he went to work upgrading the woodyard's fleet to SENNEBOGEN 830 M-T log handlers. Since then, the yard has been attracting attention for the durability of its machines, as well as the dependability of its service.
It's not surprising that McKay's first SENNEBOGEN recently turned over 42,350 operating hours. The machine is even running with its original Cummins engine. In fact, all of its original frame and components are still intact. And it's still pulling regular shifts at the Louisiana-Pacific (L-P) specialty board mill across the road from the woodyard.
But the real testament to McKay's uptime program? He can say the same thing about all six 830s he now has in service. Another of his SENNEBOGEN machines has over 41,000 hours while three others have clocked more than 30,000 hours.
"They're bulletproof," he said.
Purpose-Built for Job
Constantino Lannes, the president of SENNEBOGEN LLC, cites McKay's fleet as a prime example of what can be achieved by "thinking beyond the machine." Lannes said that well-engineered, well-constructed machines are just one element in SENNEBOGEN's commitment to long life and low total cost of ownership.
"Our investment to support our machines after the sale is equally important, along with the commitment of owners, like Larry McKay, to protect their investment in the equipment."
All of the log loaders at Mountainside Unloading work hard, long shifts. But it's work that the 830 M-T is built for, with its undercarriage specially modified for trailer-pulling and its elevating Maxcab to help operators work quickly and safely. Each axle is driven by its own transmission, delivering powerful 4-wheel drive capable of hauling 100,000-lb. log trailers, often through muddy yard conditions.
"It's not like pulling on pavement. Sometimes we're pulling in a foot of mud and deeper, and we pull a big load of wood and they just yard'er out of there," McKay said.
No Interruptions
McKay has the machines on rotating, day-long shifts unloading trucks, stockpiling the yard, and feeding wood at the mill. L-P is finishing close to a million board feet of product every day, and McKay makes sure that the process is never interrupted by problems in the woodyard.
"They go 24/7, but you know, we really never have to shut them down because of our equipment; maybe for minutes on a rare occasion. Things do break like that: you're just sitting there, and then you go to move, maybe a little coil will fail. It's happened. And so, we've kind of adapted so that we do not get ourselves in a pickle with a machine down."
On top of stocking his own parts, McKay can also rely on his dealer parts and overnight delivery even though he is almost six hours away.
"They have always been there when we needed them."
SENNEBOGEN prides itself on engineering for uptime, including features like automatic central lubrication as standard equipment, 3-micron oil filtration, reversible cooling fan, and a unique longitudinal engine mount for efficient flow-through cooling.
Planning for Uptime
The best cure for downtime, of course, is prevention. And this is where McKay's fleet management truly shines.
"When they're running, we get them to the shop once a day. Two machines come in and two machines go out. They get normal day-to-day stuff: cleaned, greased, checked over, engine oil. The pins on that first loader are still like new. And you know, they just keep running. I don't like shutting them off in the millyard.
"We add fuel conditioner once a day at the shop and I truly believe in that. It's so important to use good stuff. I use good 5:40 engine oil and really good hydraulic oil. Like, 90 percent of the hoses are still original, and there are a lot of hoses on these machines. Manuals say you should change all your hoses at 6,000 hours and a lot of these are original at 40,000 hours. I take it to be the good oil I'm using. It has an additive that keeps the rubber flexible and pliable, and we've been having very good luck with it. It's well worth a little extra, you know, to run a good oil.
"Every 250 hours, we pull them through the shop for more intensive servicing like new air filters and so on. We do regular oil analysis, and based on that, we will go 750 hours for an oil change. The little Cummins engines have been top notch. The first machine has the original engine and at 35,000 hours, I put in new fuel injectors and a new fuel pump, and it's still running great."
McKay's PM plan looks deeper and further ahead than most fleets. He has replaced the operator seats twice ("they spend 12 hours a day up there!"). Before too much longer, he expects to schedule replacements for the main boom pin and main hydraulic pump for each machine.
"It'll just be a swap-out because there's no reason these loaders shouldn't last 100,000 hours. They're just built good."
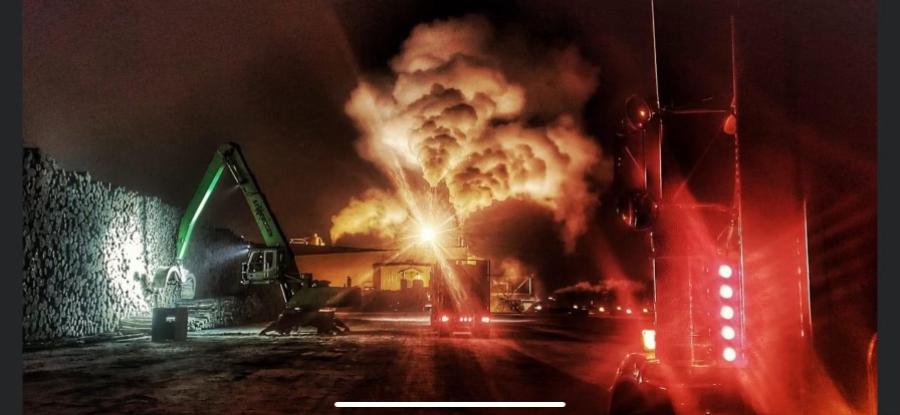
Trucks arrive and need to be unloaded. The process never stops.