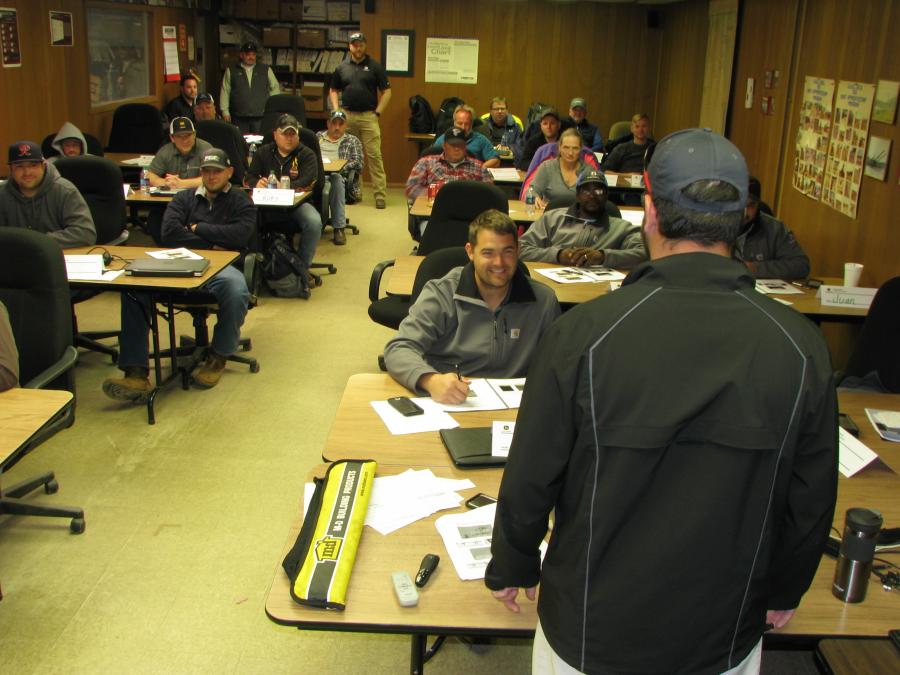
Mon March 12, 2018
Forestry Equipment Guide
Flint Construction & Forestry Division hosted a three-day technology training program from Jan. 30 to Feb 1 at the Local 926 Operating Engineers Training Facility in Ellenwood, Ga. A total of 28 attendees from 11 different companies from the United States and Canada were hosted by Tim Houchens, Flint's integrated solutions manager, and John Deere training staff members from John Deere WorkSight technology solutions, based in Davenport, Iowa.
The first two days of training concentrated specifically on GPS fundamentals, with GPS base and rover and setting up a job site. Day three was a recap followed by demo time with the new John Deere 650K, 700K and 750K dozers with integrated SmartGrade technology.
Program participant, Lynn Kent, grading engineer of JR Hayes Corporation, a mass excavation company based in Maple Valley, Wash., readily identified with the advantages of grading with GPS technology and the new John Deere SmartGrade products. Her responsibility is to take the knowledge and training experience she gains and to go back to Washington and train the operators at her company.
“Our company always looks toward being involved with the latest technology and I'm excited to have this opportunity to learn,” said Kent. “It's a tight market out there and we look towards these technologies to make us more competitive on bids.”
When asked about the training, Kent said this program is “awesome.”
“John Deere sends out some extremely knowledgably people to teach us and have the answers to all of our questions. They even ask us what they can do to better meet our needs and help us in our companies. It's been great.”
B.J. Bauman, a WorkSite Solutions instructor of John Deere, based in Davenport, Iowa, said these training sessions are geared toward customers from a broad range of expertise — from novice to advanced.
“We spend the first two days on grade management, which is the base and rover set-up and how to justify the return on investment for the system, said Bauman. The final day is operating time for machine control, trouble shooting, and getting the overall project from the data collector into the machine to make it work as a total package. Training customers is a passion of ours at John Deere. Educating and getting to know our customer's business is our way to find out how we can better support them. This is always a great event for us, our dealer, and for our customers.”
CEG